Anatomy
of a Quality Embroidery Design
When I first got started
with my embroidery machine I didn't know anything about designs.
All I knew is that some of them were very expensive and others were
free. Some seemed easy to sew and others gave me trouble:
the fabric bunched up or the satin stitch was skinny and didn't grip my
applique fabric well. Some of them were very pretty and
professional-looking while others looked sloppy and choppy. Some
of them left with me with a colorful web of jump stitches to trim or left me
wondering "why did this design just do that?" It was after I made
my own list of qualities that make up a good design that I decided to
start learning to create my own designs.
Eight years of
digitizing experience (and still learning every day!), lots and lots of
practice, classes from dealers, college-level classes, conversations
with other digitizers and thousands and thousands of designs all go into
this list of what to look for and what to avoid.
I love creating embroidery
designs and I especially love creating designs that are the best
quality. So good that you can tell the difference right away.
I wholeheartedly believe that the stitching experience is just as
important as the finished product! I am very thankful for the
amazing, positive feedback that I receive from customers who can tell
the difference. Along with the positive feedback often comes "Now
that I know what a good design is, I don't want to stitch anything less.
How can I recognize a high quality embroidery design? Are there
any signs of a poor design that I can look out for when shopping?"
I'm going to do my best to
show you some things to look for.
Most of these criteria are
agreed on by 99% of experienced digitizers. Some are personal
preferences that I think you will find helpful.
Please keep in mind that different
digitizers have different ways of doing things so there is not a set
"right way" and "wrong way", but experienced digitizers will agree that
some qualities are absolutely necessary when creating a good design,
regardless of technique or personal preference.
Let's get started with the
basics...
What is digitizing?
Digitizing is the art of creating design files that are read by
embroidery machines.
What is a digitizer?
A
digitizer is someone who creates design files. A digitizer can
create files from their own artwork or they can use commercial clipart
to base the designs on.
What is digitizing software?
Digitizing software is a computer program that the digitizer uses to
create design files. The digitizer must use the software to
communicate with the machine. We must tell it where to stitch, how
to stitch, in which direction, in which order and which color. We
tell it when and where to start and when and where to stop and how close
together to place the stitches. There
are too many factors to list. A digitizer has many, many elements
to consider when creating a design. Different digitizing software
packages allow different types of control over a design. Some are
very simple and aimed at home-based embroiderers and hobbyists while
others are very technical and are aimed at embroidery and digitizing
professionals. In this article I will use Brother's PE-Design as
an example of home-based software and Wilcom's Embroidery Studio 2 as an
example of professional software.
When I first started
embroidering, I thought that I could simply find an image on the
internet and send it to my machine and that somehow my machine would
instinctively know exactly what to do. It wasn't long before I
realized that this is FAR from true! A digitizer must take the
image and re-draw it using commands that an embroidery machine can
understand. We can't simply convert an image file to an embroidery
file. Well...there are programs that will do that but let me show
you why this very rarely yields good results. Taking an image file
and using software to automatically create and embroidery file is called
Auto-Digitizing.
Auto-digitizing does not
allow the digitizer to control the design. We can't tell it where
to start and stop or which direction to stitch or which type of stitch
to use. Adjustments can me made but it is usually more
time-consuming to fix an auto-digitized design than it would be to
simply start from scratch. I'm going to use high-quality
commercial clipart of a zebra throughout this article to illustrate
different digitizing results.
In this example I
ran the zebra image through Brother's PE-Design Software. I used
the "image to stitches" function.
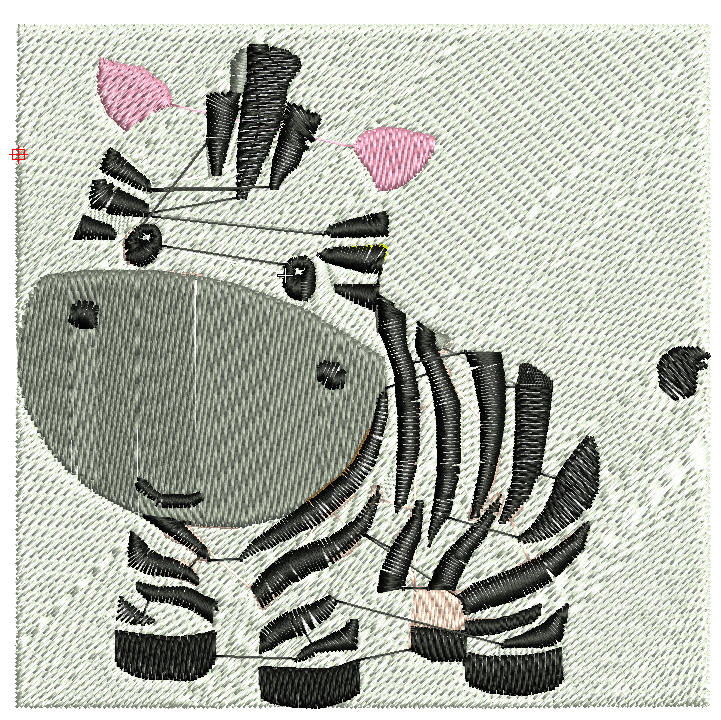
The results are nothing
short of terrible. (You can download this disaster
HERE if
you would like to see for yourself)
So, what wrong with this
design? First of all, it isn't very nice-looking. There
isn't much definition. The stitches appear choppy and gapped.
There are some other flaws that you can't see here but that will
absolutely contribute to the poor quality of this design. Look at
the white background area that the software added. This should be
negative space (nothing there). The stitches are running at
different angles and are different lengths. THERE IS NO UNDERLAY
STITCHING ANYWHERE <--BIG Problem!
What is underlay stitching?
Underlay stitches are stitches that run before a block of stitching.
They are usually more widely-spaced than fill stitches. Think of
the underlay stitches as your foundation. They are there to
support the stitches and prevent the design from shifting, puckering,
and many other disastrous outcomes (think hole in a tee shirt!).
You don't want to build a house without a foundation.
Let's look at the black.
First, it is full of jump stitches.
What are jump stitches?
Jump stitches are the long stitches that run when the machine stitches
in
one area and then picks up and moves to start stitching in a different
area. Some machines will trim these stitches for you.
A skilled digitizer will
minimize jumps by telling the machine to make the smallest jumps between
objects. We must sequence the elements of a design so the they
stitch in order by how close they are to each other. Think about
crossing a river by stepping on stones. You are going to want to
step to the next closest stone, not take one giant leap forward over
five stones and then three backward and two forward, right? Almost
all of the long jumps in this design could be minimized. I'll
explain more about that later...
Still looking at the
black...look at the way the stitch angles change direction and how the
stitch types are different. Some are a fill stitch (the stitch
type you see in the white background area) while some are satin stitch,
the smoother stitching that you see on some of the stripes,
inconsistently. The stitch areas are broken up into chunks rather
than continuous, free-flowing shapes. A good example would be the
eyes.
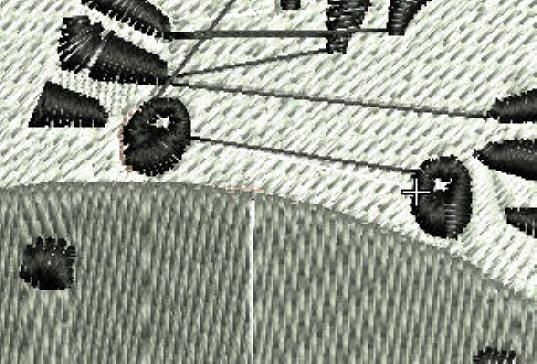
The software added some
yellow in there as well as some brown on the side of the face and pink
under some of the stripes. There are 72 color changes in this
design! I don't think I need to explain what a pain THAT is!
There are many other issues with this design, too many to describe.
Overall
results? Terrible (in my opinion).
Next, I ran the same image
through Wilcom's Embroidery Studio 2 "Smart Design".
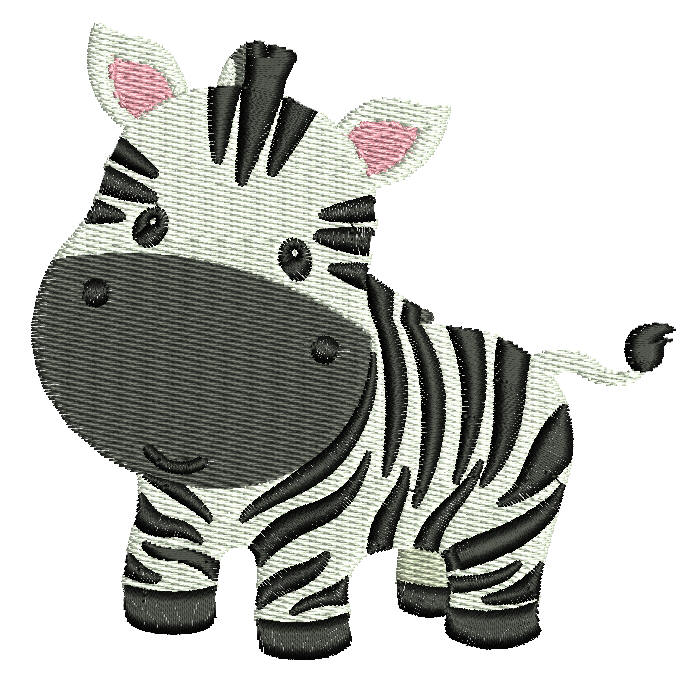
The results are not as
unattractive as the first auto-digitized design but this is still FAR
from a quality design.
(You can download this
less-than-quality design
HERE) The scary thing about a design like
this is that you might actually purchase a design that looks like this!
It's not so terrible that you would write it off as a "bad design" right
away.
So, what wrong with this
design? Again, THERE IS NO UNDERLAY STITCHING ANYWHERE <--BIG
Problem! You're going to get shifting
and gaps and thread breaks. You don't want to build a house without a foundation.
The angle of the white,
pink, and grey stitches is the same. All of the stitching is
running in the same direction! <--Another BIG Problem!
What are stitch angle and direction and why do they matter?
Stitch angle is the direction that the stitches are placed, horizontal,
vertical, and every angle in between. Different angles products
different effects. Stitch direction is the direction that the
stitches run as they sew. Start on the upper left, end on the
lower right, start on the lower right end on the upper left, or some
designs will start on one side and fill partial areas and then travel to
the other end and change direction to come back and meet in the middle.*
*My personal preference is
to avoid designs that do that because they tend to gap where the
stitches meet, especially if the filled stitch area is large.
Sometimes it is an intentional move by the digitizer to minimize a jump
stitch but many times it is a
software default that the digitizer didn't take the time to replace with
his/her own settings.
Stitch direction is also important because a design must
have balanced angles and directions to avoid shifting and bunching.
If all of a design's stitches run at a 45 degree angle from left to
right then there is going to be a lot of left to right, top to bottom
movement in the hoop. If the designs has outlines or details they
will most likely be off, and it can cause some distortion of the
design's shapes.
If you see a design that
has the same angle on all of the stitches then I would say it is safe to
assume that the stitch directions are also going to be automatic or all
the same and I, personally, would avoid that design.
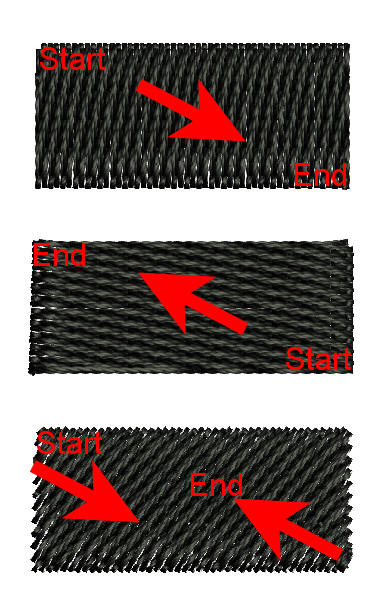
Again, we have some choppy
and uneven areas in the pink part of the ears. There are also some
jumps within the same color which are totally unnecessary and
unavoidable and, once again, the solid eyes are broken up into chunks
rather than continuous, free-flowing solid shapes.
The black stripes and tail
are all satin stitch and some of them appear to be too wide to use a
satin fill. Some machines won't stitch wide satin stitches and
they can also snag easily. Those areas should be a split satin,
where the machine will make some extra stitches to keep the stitch
length shorter in the wider parts. The one time you DO NOT want to
see satin stitches split is on a satin applique border. That means
the satin outline is too wide.
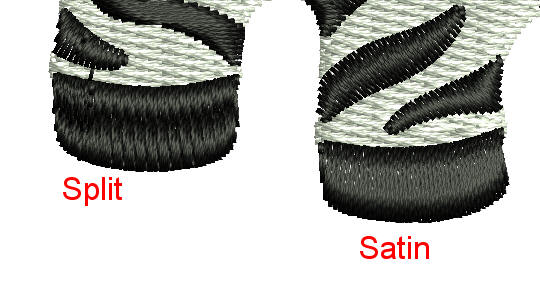
Overall
results? Bad, but possibly usable with lots of cleaning up (in my
opinion).
On to the next...
I used Brother's PE-Design
software to manually digitize the same zebra in applique form, and I did
the sloppiest job I possibly could! Just a little note...PE-Design
is a full digitizing program and it is actually the first program I
started with, but it is VERY limited in what you can do with a design.
I think it is great software for personal use but not professional use
(personal opinion). If you do decide to give it a try (it is very
simple and easy to learn as far as digitizing software goes) keep in
mind that its tie offs are poor and you will need to manually draw lock
stitches, it doesn't render curves or corners well but you can work
around that with the manual punch tool and extra nodes and I always
manually drew my underlay stitches as well. A good, very experienced
digitizer can work around software limitations. That being said, I
didn't take any of those extra steps in my example of poor digitizing.
(You can download this sloppy applique design
HERE)
Let's take a look at what
I threw together in about 30 minutes:
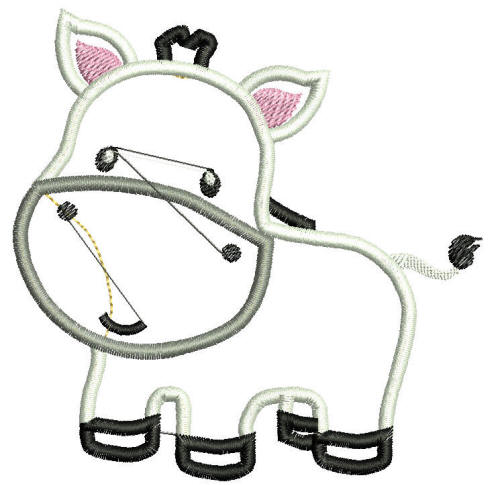
We'll look at it piece by
piece. First are the placement and tack down stitches. I
intentionally left these sloppy with overlapping pieces.
Overlapped fabrics can show through and cause thick, uneven areas for
the machine to stitch over. Most of the time these can be
eliminated.
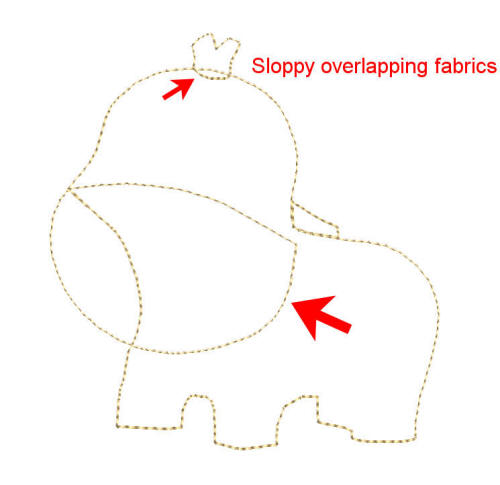
Next are the ear details.
This step has no underlay and an unnecessary jump that can
be eliminated. In applique designs you really shouldn't see any
jumps in the first few layers, especially in the satin outlines.
They can almost always be eliminated with some extra effort from the
digitizer. Jumps between eyes or within detail steps that stitch
last are normal and can't be avoided. Jumps early in a design,
especially within the satin steps, are telltale signs of a design that
was put together quickly (make more designs, sell more designs!) or
possibly the work of an inexperienced digitizer. Most of the time
they can be trimmed and you will never know they were there but why make
more work for the embroiderer and slow the machine down since it has to
stop and tie and trim and jump and then move on to the next part of the
design? I prefer to keep it flowing.
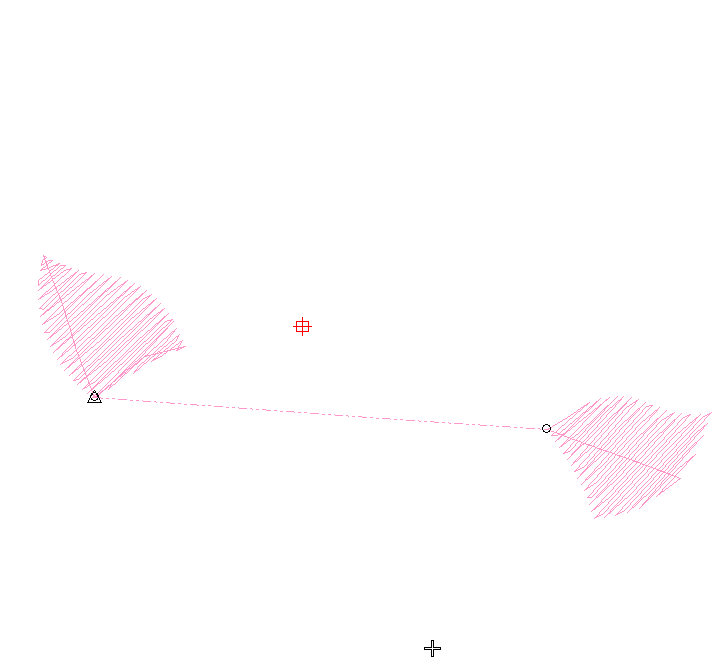
Next are the black
details. Again, no underlay, the satin applique outlines are too
thin and multiple unnecessary jumps which can almost completely be
eliminated. The mouth is sloppy with open, boxy ends. All of
the details are the same stitch direction and angle. The mane and
hooves are very tiny pieces of fabric that would work better in a filled
stitch and the way PE-Design rendered the corners is odd and not
visually appealing. Those
overlapped corners are unattractive and are hard on your machine, not to
mention bulky where the threads sit on top of each other.
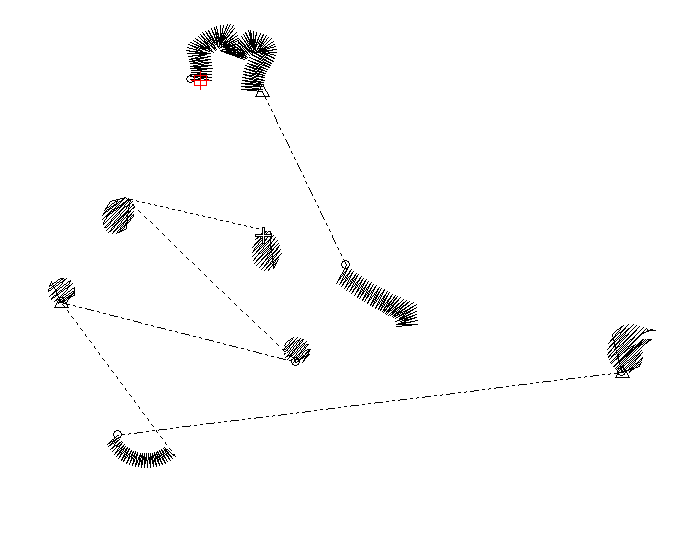
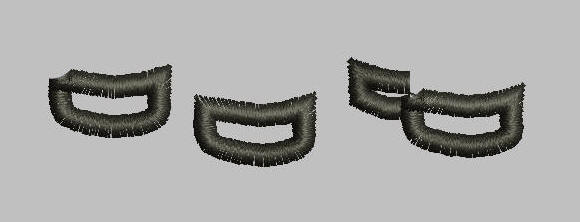
Next is the white satin
outline. This is a total disaster!! ALL of these jumps can
be eliminated with the exception of the whites of the eyes. Again,
no underlay, satin is too thin. Filled areas are the same angle
and direction.
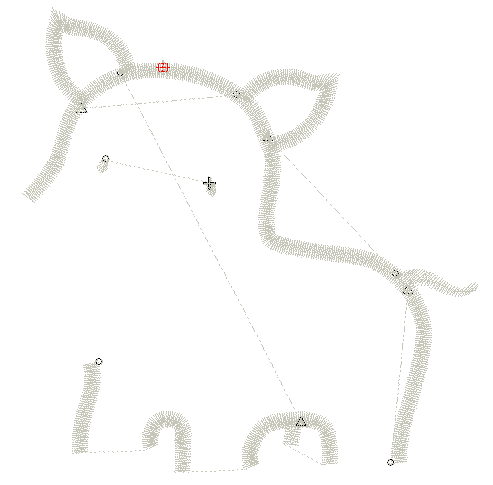
Last we have the snout.
Is that what it's called on a zebra?! Anyway, the satin is too
thin and there is no underlay. Also, see how it looks kind of
wobbly and wonky? That's how PE-Design renders curves and I didn't
bother to clean it up.
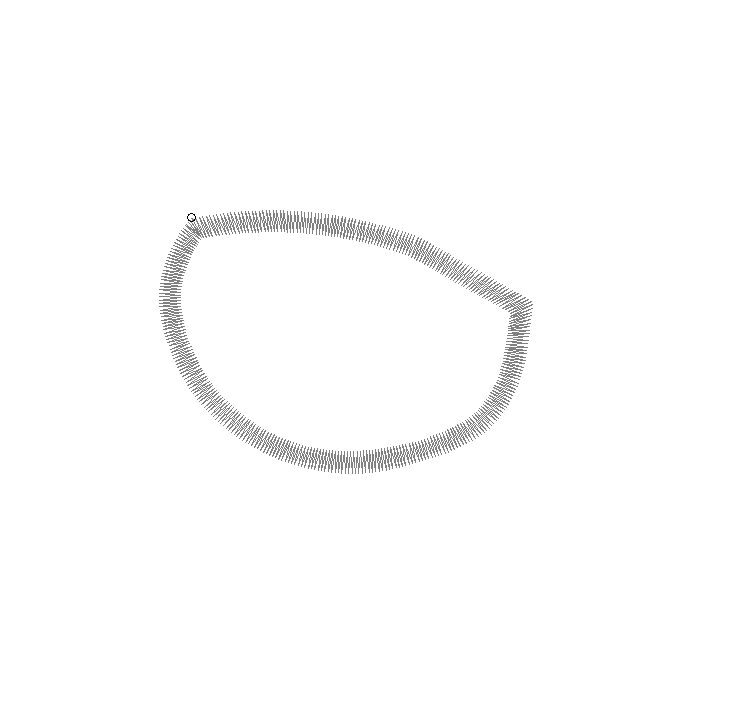
Let's take one last look
at this example of a BAD design.
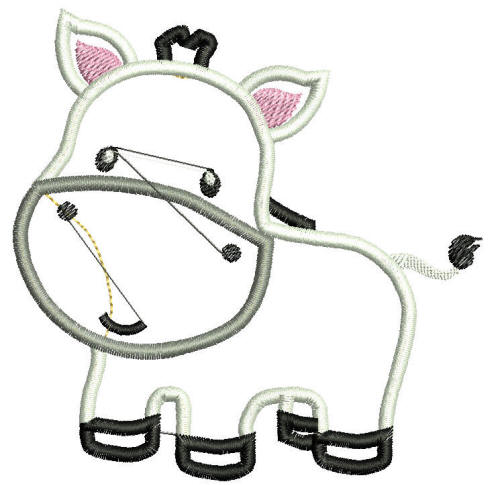
And here is the finished
design.
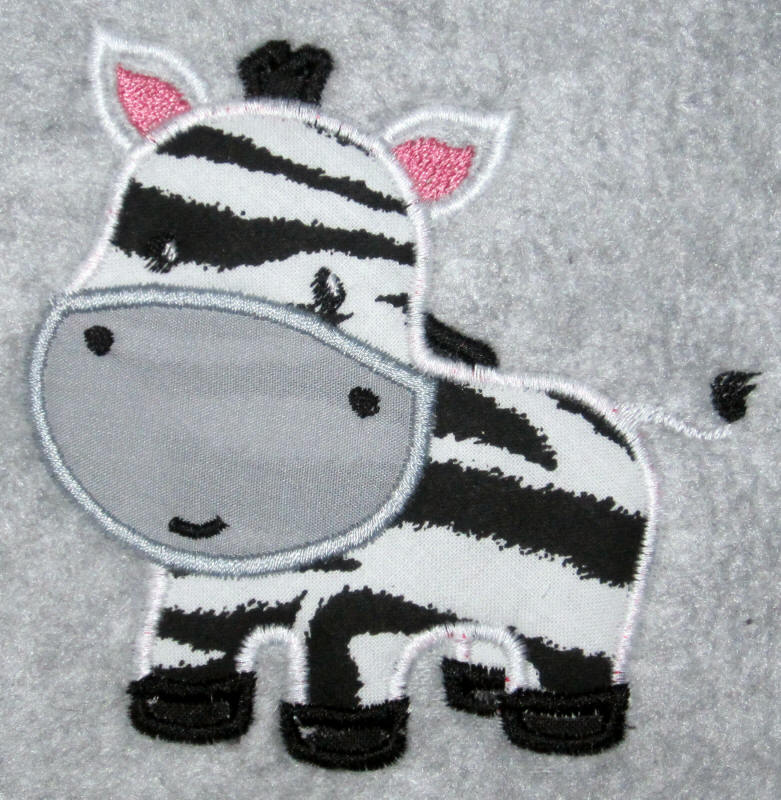
Surprising, isn't it!
You probably thought it would look much worse. This scares me because I might
purchase a design based on a photo like this if I didn't know better. This was a nightmare
to stitch. It jumped all over the place so my machine was stopping
a lot and I had some shifting since there was no underlay. Also,
the tie-offs are inadequate and I had a LOT of unraveling. My tack
down stitches unraveled so the fabric wasn't secured well and there were
loops at the beginning of all of the satins because the tie-in was just
not good, only two stitches! The lack of a good tie-in also caused
loops on the mouth. The hooves shifted a bit which left one edge
of the fabric completely exposed.
The fabric will probably pull out from under that thin satin (remember,
this design has NO underlay). This is a good example of how a
decent-looking
finished design has nothing to do with the quality of the design. A terrible design can actually look OK
when finished. It doesn't make it any less terrible, though!
This design was very unpleasant to stitch and will not hold up over
time. I doubt it would last through one wash on a T-shirt.
Last but not least, I
manually digitized the same zebra clipart in Wilcom Embroidery Studio 2
and I took all of the extra steps to make this design stitch out great.
Not only is the finished product going to look awesome, this design is
going to be easy and stress-free to stitch!
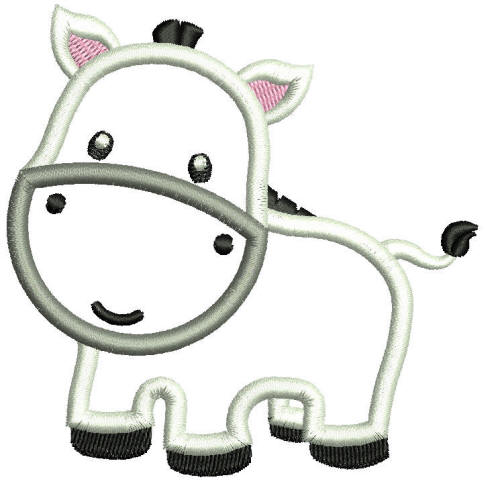
Let's look at some of the
features that make this design a good one.
No overlapping fabric pieces.
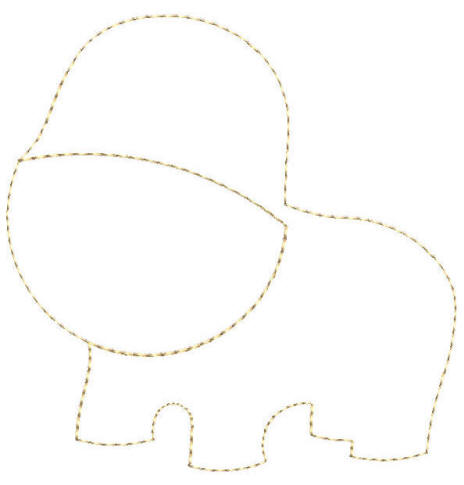
No unnecessary jump stitches.
The ONLY jumps in this design are between the facial features. And
folks, WE HAVE UNDERLAY! A good design rests on a good foundation.
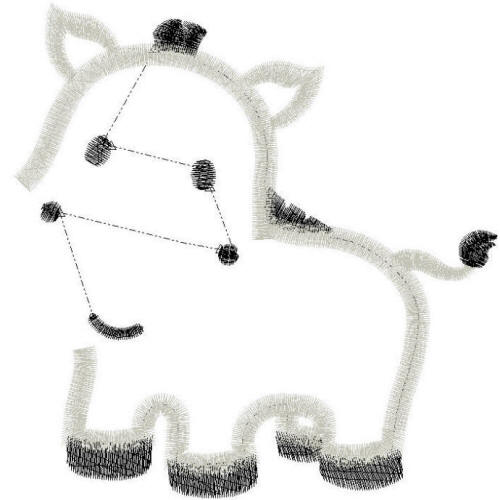
The satin stitches are wide
and the design is smooth, not wobbly and wonky looking. The teeny
tiny applique pieces have been changed to fill stitches. The fill
stitch areas have appropriate stitch angles and push and pull
compensation applied. No shifting, no gapping, no bunching.
The mouth is rounded out and smooth. No more chop-block ends.
The mane and tail have cute details enhanced.
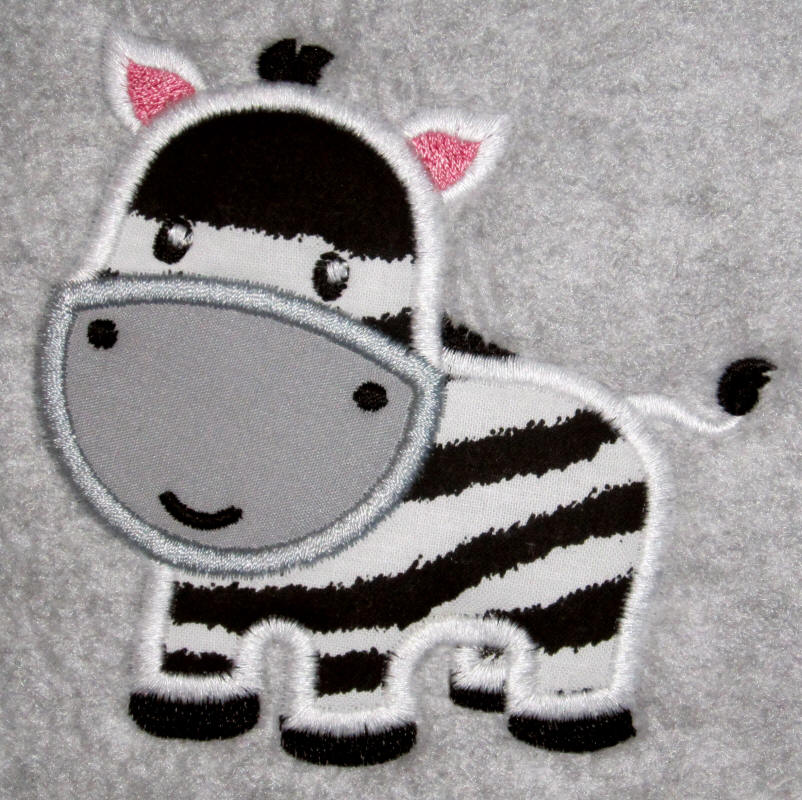
In a nutshell, this design
has been properly sequenced to minimize color changes, jump stitches and
overlaps, a variety of stitch types and angles are used to balance out
the push, pull, and flow of the design, underlay is a strong foundation,
wide satin stitches secure your fabric and it's CUTE! (You can
download this adorable and easy-to-stitch applique design
HERE)
I hope this helps to
explain what to look for and what to avoid when looking for quality
applique and embroidery designs. There is so much more information
that I don't have room or time to type out! Here are some
side-by-sides to help you compare:
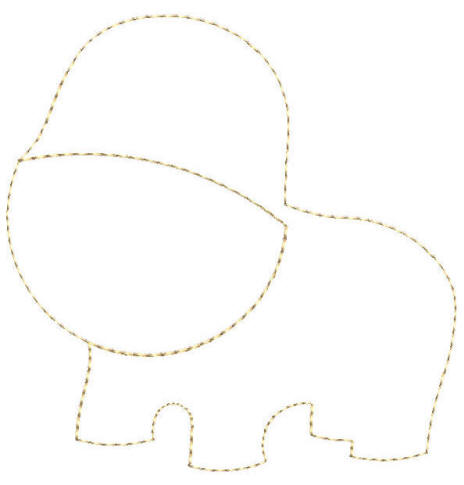
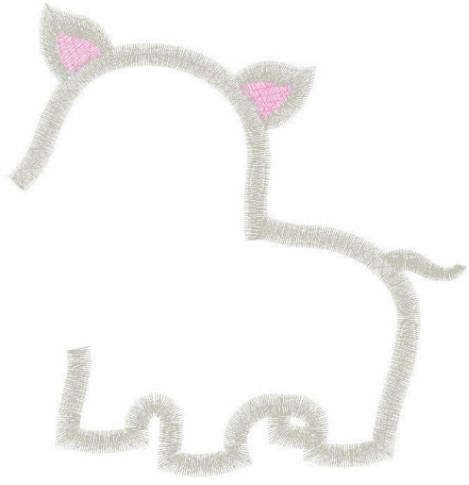
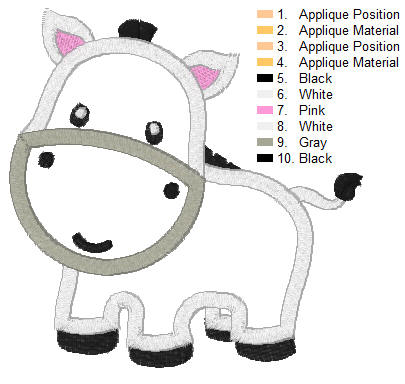
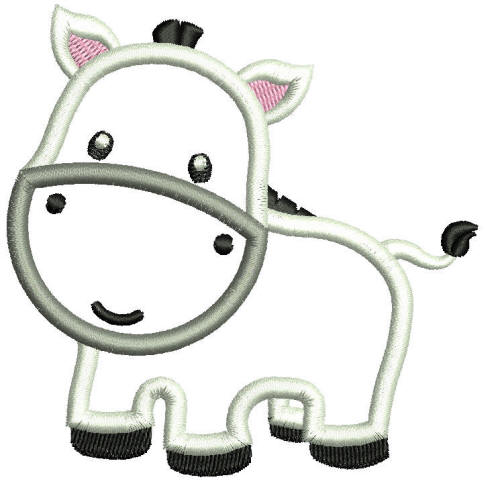
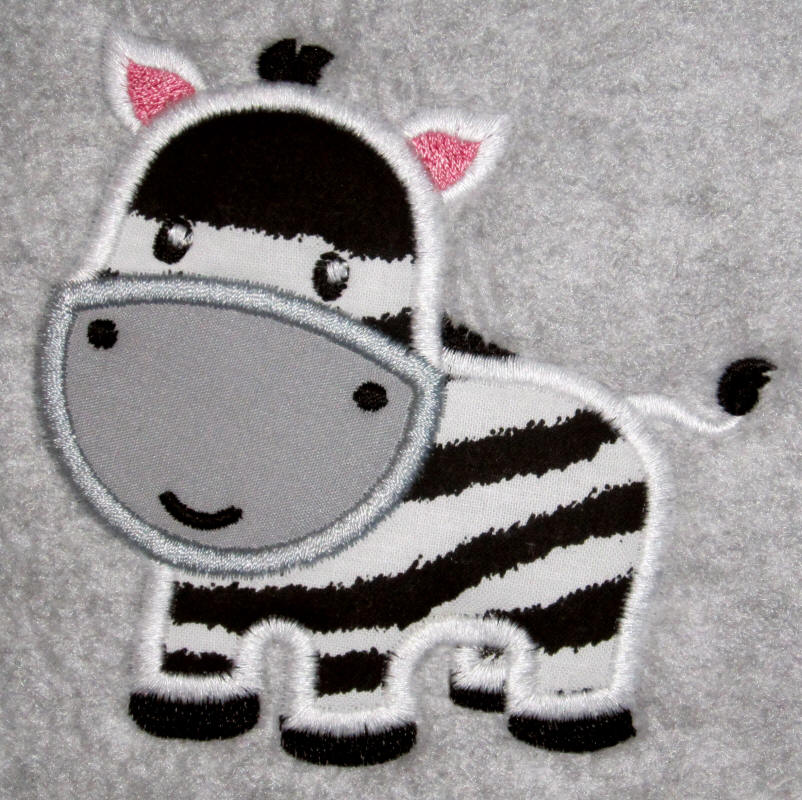